Codes of typical errors in Viessmann gas boilers

Why errors appear on Viessmann gas boilers and what they mean
Unlike old-fashioned gas water heaters and primitive semi-handicraft parapet boilers, modern water heating and heating installations (to which, without a doubt, Viessmann brand equipment also belongs) are controlled by electronics. The electronic "brains" of the boiler during operation receive information from a variety of sensors and control a huge number of operating parameters in order to ensure the most efficient and safe combustion of gas fuel and maintain the temperature in the circuits at a given level. But power surges in the mains, fluctuations in gas pressure in the line, clogging of the chimney, the formation of soot and other factors (from careless operation to defects in individual parts) lead to the fact that the boiler may fail. Detecting an error that affects the flow Rate of the boiler or the safety of its operation, the electronics warns users (sometimes the device turns off if the problem is considered critical). For Viessmann boilers, malfunctions are displayed on the display with a flashing code. Knowing what the error code means, the customer or service technician can take corrective action and return the equipment to a healthy state.
Viessmann Vitopend boiler error codes
The Viessmann Vitopend family includes several models of gas boilers. They differ from each other in terms of power, type of combustion chamber (the boiler can be chimney or turbocharged), the number of serviced circuits (there are single- and double-circuit devices) and the type of controller (electronic control unit). But they have a common system for designating errors using conditional codes.
![]() |
Vitopend 100-W boiler controls (type WH1D). |
This table shows the codes of typical errors that owners of different generations and models of Viessmann Vitopend boilers can see on the displays of their devices during the operation of the equipment.
Display | The code | Decryption |
---|---|---|
![]() |
06 | Insufficient amount of water. The heating medium pressure in the circuit is too low (less than 0.8 bar). It is required to add water and return the pressure gauge needle to the green zone. |
![]() |
0A | Gas pressure too low. Make sure that the gas pressure in the line is correct. Check pressure switch. |
![]() |
0B | |
![]() |
0C | Mains voltage too low. Check the electrical network. |
![]() |
CC | There is no communication between the controller and the external expansion module. Check the connecting cable and pins of the outdoor unit. |
![]() |
F2 | Temperature limiter triggered. The limiter switched off the burner due to too high heating medium temperature. You should start by checking the restrictor and its cable. If they are working, you need to check the level of filling the installation with water, and also make sure that the circulation pump is working and has no air locks. |
![]() |
F02 | |
![]() |
F3 | A flame is detected even before the burner starts. The ionization electrode and its cable should be checked. |
![]() |
F03 | |
![]() |
F4 | The flame is not recognized. There is no signal from the ionization electrode. It is necessary to check the electrodes with their wires, the gas pressure in the line and the condition of the gas shut-off valves, as well as the ignition module. |
![]() |
F04 | |
![]() |
F5 | Pressure switch failure. The pressure switch does not open when the burner is started or does not close when the ignition load is reached. It is necessary to check the relay with all cables and hoses leading to it. |
![]() |
F05 | |
![]() |
F08 | Gas valve relay failure. The solenoid valve, relay and connecting cables must be checked. |
![]() |
Boiler controls Vitopend 100-W (type A1JB). |
A significant part of the error codes that appear on the displays of Viessmann Vitopend boilers are related to sensor malfunctions. The reason most often is a short circuit that caused damage to the sensor, or the absence of a signal due to a broken wire or damage to its insulation. All such problems involve checking the sensors and the wire bundles leading to them.
Display | The code | Decryption |
---|---|---|
![]() |
F10 | Short circuit of one of the temperature sensors (outside temperature or indoor temperature). |
![]() |
F18 | There is no signal from one of the temperature sensors (outside temperature or indoor temperature). |
![]() |
F30 | Short circuit of the boiler temperature sensor. |
![]() |
F38 | No signal from the boiler temperature sensor. |
![]() |
F50 | Short circuit of the tank temperature sensor. |
![]() |
F51 | Short circuit of the outlet hot water temperature sensor. |
![]() |
F58 | No signal from tank temperature sensor. |
![]() |
F59 | No signal from outlet hot water temperature sensor. |
![]() |
F70 | Short circuit of the collector temperature sensor. |
![]() |
F78 | No signal from the collector temperature sensor. |
![]() |
F80 | Short circuit of the lower tank temperature sensor. |
![]() |
F88 | No signal from the lower tank temperature sensor. |
![]() |
F90 | Short circuit of the upper tank temperature sensor. |
![]() |
F98 | No signal from upper tank temperature sensor. |
Viessmann Vitodens boiler error codes
Heating systems that belong to the Viessmann Vitodens family are modern gas condensing boilers. They are technically sophisticated devices, "hung" with a variety of sensors and actuators, with the help of which the electronics control the operation of the boiler.
The Viessmann Vitodens family includes several generations of condensing boilers. Since technology does not stand still, different generations were equipped with different electronic controllers and differed from each other in front panels with displays and sets of controls. Older versions of Viessmann Vitodens condensing boilers have simple LCD displays that show error codes as two letters or numbers.
![]() |
The small LCD display can only display a limited number of symbols and icons. |
The table below shows the main error codes that can be seen on the displays of the Vitodens 050-W boilers (types BPJC and BPJD), Vitodens 100-W (types B1HC, B1KC, WB1C and WB1B), as well as Vitodens 200-W (types B2HA and B2KA).
Problems associated with short circuits of sensors or the absence of signals from them require checking both the sensors themselves and the bundles of wires going to them for breaks or damage to the insulation. For other types of faults, short instructions are given on where to look for problems.
Display | The code | Decryption |
---|---|---|
![]() |
0A | Increased concentration of Cooling system. The carbon monoxide detection relay has tripped. It is necessary to check the boiler and eliminate the cause of Cooling system emission before restarting. |
Reduced gas pressure. The relay has tripped, indicating that the gas pressure in the line is below normal. The gas supply should be checked. | ||
![]() |
0C | Undervoltage in the network. The voltage in the power supply network is below normal. The power supply needs to be checked. |
![]() |
ten | Short circuit of the outdoor temperature sensor. |
![]() |
eighteen | No signal from outside temperature sensor. |
![]() |
twenty | Short circuit of the supply temperature sensor. |
![]() |
28 | No signal from flow temperature sensor. |
![]() |
thirty | Short circuit of the water temperature sensor in the boiler. |
![]() |
38 | There is no signal from the water temperature sensor in the boiler. |
![]() |
fifty | Short circuit of the tank temperature sensor. |
![]() |
51 | Short circuit of the outlet hot water temperature sensor. |
![]() |
52 | Short circuit of the volumetric flow sensor. |
![]() |
58 | No signal from tank temperature sensor. |
![]() |
59 | No signal from outlet hot water temperature sensor. |
![]() |
5A | No signal from volumetric flow sensor. |
![]() |
90 | Short circuit of one of the temperature sensors. |
![]() |
91 | |
![]() |
92 | Short circuit of the collector temperature sensor. |
![]() |
93 | Short circuit of the cylinder temperature sensor. | ![]() |
94 |
![]() |
98 | No signal from one of the temperature sensors. |
![]() |
99 | |
![]() |
9A | No signal from the collector temperature sensor. |
![]() |
9b | No signal from cylinder temperature sensor. |
![]() |
9C | |
![]() |
A3 | Flue gas temperature sensor installed incorrectly. |
![]() |
A7 | The control panel is defective and needs to be replaced. |
![]() |
A9 | No signal from the Open Therm thermostat. |
![]() |
b0 | Short circuit of flue gas temperature sensor. |
![]() |
b7 | Burner malfunction. It is necessary to completely disconnect the boiler from the network and turn it on again. |
![]() |
b8 | No signal from flue gas temperature sensor. |
![]() |
dA | Short circuit of the temperature sensor in one of the heating circuits. |
![]() |
db | |
![]() |
DC | |
![]() |
dd | There is no signal from the temperature sensor in one of the heating circuits. |
![]() |
dE | |
![]() |
dF | |
![]() |
E3 | No signal from the temperature limiter. |
![]() |
E5 | Internal error associated with a malfunction of the ionization electrode. |
![]() |
F0 | Internal error related to controller failure. |
![]() |
F1 | Flue gas temperature too high. The water pressure in the system needs to be checked. You also need to check if the circulation pump is working and if there is air in it. |
![]() |
F2 | Temperature limiter triggered. It is necessary to check the pressure in the boiler, the condition of the pump, the temperature limiter and the cables leading to them. |
![]() |
F3 | A flame is detected even before the burner starts. The error appears due to a malfunction of the ionization electrode or damage to its cable. |
![]() |
F4 | The flame is not recognized. The error may appear due to a malfunction of the electrodes and their cables, low gas pressure in the line, or malfunctions associated with incorrect operation of the gas regulator, steam trap, or ignition and ignition modules. |
![]() |
F8 | The fuel valve closes with a delay. It is necessary to check the fittings regulating the gas flow and the control cables. |
![]() |
F9 | The fan rotates too slowly. The fan, connecting cables and controller need to be checked. |
![]() |
FA | The fan did not stop. You need to check the fan, its controller and the power and control cables connecting them. |
![]() |
FC | The fan controller is defective. You should check the controller and the wires connected to it. |
![]() |
fd | Burner malfunction. The ignition electrode and connecting cables must be checked. This error also often appears due to strong electromagnetic interference acting on the boiler electronics. |
![]() |
FF | |
![]() |
Communication error between burner and control panel. |
![]() |
Boiler display Viessmann Vitodens 050-W (type B0KA). |
Viessman Vitodens condensing boilers of the latest (as of 2022) generations are equipped with more modern versions of controllers that can analyze a much larger number of parameters and control modules with large graphic displays or even 7-inch color touch screens. These models of boilers use a completely different system for indicating errors.
The table below shows the codes for the most common boiler errors Viessmann Vitodens 050-W (types B0KA and B0HA), Viessmann Vitodens 100-W (types B1HF and B1KF), Viessmann Vitodens 111-W (type B1LF) and Viessmann Vitodens 200-W (types B2HF and B2KF).
Display | The code | Decryption |
---|---|---|
![]() |
5 | Open or short circuit of the volumetric flow sensor. |
![]() |
7 | No signal from tank temperature sensor. |
![]() |
eight | Short circuit of the tank temperature sensor. |
![]() |
eleven | No signal from the collector temperature sensor. |
![]() |
12 | Short circuit of the collector temperature sensor. |
![]() |
13 | No signal from outside temperature sensor. |
![]() |
fourteen | Short circuit of the outdoor temperature sensor. |
![]() |
29 | No signal from hydraulic separator sensor. |
![]() |
thirty | Short circuit of the hydraulic separator sensor. |
![]() |
49 | No signal from flue gas temperature sensor. |
![]() |
fifty | Short circuit of flue gas temperature sensor. |
![]() |
57 | No signal from the room temperature sensor. |
![]() |
58 | Short circuit of the room temperature sensor. |
![]() |
59 | Undervoltage in the network. The voltage in the electrical network is below the permissible level. You need to check the network. |
![]() |
62 | Overheat. The safety temperature limiter has tripped. The reasons may be insufficient water in the system, incorrect pressure in the expansion tank, malfunctions of the pump or three-way valve. |
![]() |
63 | Flue gas temperature too high. The flue gas safety temperature limiter has tripped. Such problems occur due to incorrect operation of the pump and diverter valve, as well as due to insufficient filling of the system with water. |
![]() |
67 | Incorrect signal from the flame sensor. The current from the sensor is out of range. It is necessary to check the ionization electrode and the entire gas supply system (taps, valves, relays and filters). |
![]() |
68 | A flame is detected even before the burner starts. This error is caused by malfunctions of the ionization electrode or the electronic control unit for the operation of the boiler. |
![]() |
69 | Incorrect signal from the flame sensor. The current from the sensor is out of range. It is necessary to check whether the ionization electrode is installed correctly. Problems can also be malfunctions of the gas fittings, fan unit or central electronic module. |
![]() |
70 | Internal error. Malfunctions in the control unit. If the error persists, the central electronic module may need to be replaced. |
![]() |
71 | The fan rotates too slowly. It is necessary to check the fan for blockage and the flue system for clogging with combustion products. It is also possible that the boiler is set incorrectly (the wrong type of gas is selected). |
![]() |
72 | The fan did not stop. Check the fan unit and restart the boiler. If the error persists, this assembly will need to be replaced. |
![]() |
73 | Internal communication error. If the error persists, the central electronic module may need to be replaced. |
![]() |
74 | Boiler pressure too low. The error appears due to a lack of water in the system or the formation of air pockets. |
![]() |
75 | No bulk consumption. Open the taps (filling and emptying) and add water to the boiler. The error may also be due to a malfunction of the sensor or pump. |
![]() |
87 | Boiler pressure too high. It is necessary to open the taps (filling and emptying), check the pressure in the system and the expansion tank and double-check the pressure sensor readings using an external pressure gauge to make sure its readings are correct. |
![]() |
89 | The internal pump is blocked. Check pump, replace if defective. |
![]() |
95 | No signal from the Open Therm thermostat. The OpenTherm remote control is not connected or not working. |
![]() |
176 | Accumulation of condensate in the thermal module. It is necessary to eliminate the accumulation of condensate, at the same time replacing the electrodes and the flame head. |
![]() |
182 | Short circuit of the outlet hot water temperature sensor. |
![]() |
183 | No signal from outlet hot water temperature sensor. |
![]() |
184 | Short circuit of the supply line temperature sensor. |
![]() |
185 | No signal from supply line temperature sensor. |
![]() |
299 | Incorrect date and time setting. |
![]() |
345 | Overheat. The thermal relay has tripped due to the fact that a sufficient level of heat extraction is not provided. It is necessary to check the filling of the system with water, as well as to make sure that the pump and the three-way valve are in good condition. |
![]() |
346 | Unable to calibrate ionization current. The error is due to insufficient gas pressure (due to problems with the gas fittings or filter clogging), electrode malfunction, steam trap overflow or obstruction of the smoke exhaust system. |
![]() |
347 | Flue gas recirculation. It is required to eliminate the causes of flue gas recirculation. A complete inspection of the smoke extraction system is required. |
![]() |
349 | Error in determining the mass air flow. Malfunctions can be caused by excessive contamination of the supply air, carbon deposits on the combustion head, or a defective fan assembly. |
![]() |
352 | Increased concentration of Cooling system. A complete check of the flue gas path is required. The reasons may be its leakage or clogging. |
![]() |
353 | Insufficient gas supply. The gas pressure is not enough to provide the required boiler output. The reasons may be damage to the control valve, clogged filter or pressure drop in the line. |
![]() |
357 | |
![]() |
359 | No ignition spark. It is necessary to check the ignition electrode and its wire, the ignition module and the central control unit for the operation of the boiler. |
![]() |
361 | The flame is missing or too weak. The ignition electrode must be checked and cleaned, as well as its cable and plug. |
![]() |
379 | |
![]() |
369 | The flame is unstable or goes out. The gas supply devices (taps, valves, relays), the smoke exhaust system and the ignition electrode should be checked. |
![]() |
380 | |
![]() |
371 | The fan rotates too slowly. It is necessary to check the fan and the wires going to it. |
![]() |
372 | Repeated loss of flame during calibration. Problems can be a defective electrode, loose plug contacts, a malfunctioning gas valve, a buildup of condensate in a siphon, or incorrect operation of the flue gas removal system. |
![]() |
381 | The flame is extinguished. Loss of flame during boiler operation due to gas supply problems, flue gas recirculation or electrode contamination. |
![]() |
382 | The error counter has overflowed. The counter has exceeded the allowable value. Open the error history through the menu on the control panel and unlock the boiler. |
![]() |
383 | The gas supply line may be contaminated. Problems in the operation of the gas fan, which may be associated with its malfunction, as well as contamination of the gas supply line or too low pressure in the gas line. |
![]() |
384 | |
![]() |
393 | Short circuit of the flue gas temperature sensor. |
![]() |
394 | No signal from flue gas temperature sensor. |
![]() |
416 | Incorrect position of the flue gas temperature sensor. |
![]() |
446 | Incorrect readings of the supply line temperature sensor. |
![]() |
447 | Incorrect voltage on the ionization sensor. |
![]() |
448 | Incorrect current on the ionization sensor. |
![]() |
457 | Fan blocking. The fan is blocked or too tight. Needs checking and cleaning. |
![]() |
461 | Chimney flap failure. The damper is blocked or hard to move. Requires verification and unlocking. |
![]() |
463 | Possibly air pollution. The air supplied to the boiler furnace is polluted. The flue gas exhaust system must be checked for contamination and flue gas recirculation. |
![]() |
471 | There is no signal from the pressure sensor in the boiler. |
![]() |
540 | Accumulation of condensate in the combustion chamber. The steam trap and its siphon must be checked and cleaned of dirt blocking the condensate drain. |
574 - 579 | No signals from room temperature sensors. | |
682 - 683 | Mass air flow sensor missing or defective. | |
![]() |
766 | Flue gas temperature too high. Clean the thermal module from dirt and perform its maintenance. |
![]() |
767 | |
![]() |
980 | The volumetric water flow is below the set value. The error occurs if the DHW cylinder taps are closed or the pump is defective. |
![]() |
981 | |
![]() |
982 | The pump is running dry. It is required to check the pump assembly and the membrane in the expansion tank. |
![]() |
Touch 7-inch display of the boiler Viessmann Vitodens 200-W (type B2HF). |
Please note: the tables in this article do not contain all error codes for Viessmann boilers, but only those that are used to indicate the most typical and most common malfunctions in the operation of gas heating installations of this brand. A complete table of error codes for each boiler model can be found in the documents, which are usually called "Installation and service instructions for specialists." They are posted on the manufacturer's website and on the pages of some online stores selling Viessmann boilers.
What to do if the Viessmann boiler knocks out an error
It should be noted that Viessmann does not particularly approve of the independent solution of technical problems associated with malfunctions in boilers by the hands of users. Instead, the company strongly recommends calling a service technician (on many models of Viessmann equipment, even a fault indication icon is shown along with an icon depicting a handset). Therefore, even having figured out with the help of this article what the Viessmann boiler error means, it is better to follow the manufacturer's recommendations and call a certified boiler repairman. In any case, our article should be considered solely as a source of information, and not a guide to action.
Articles, reviews, useful tips
All materials
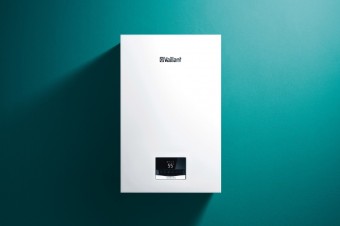
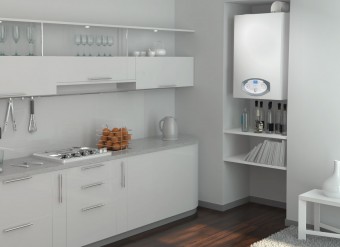


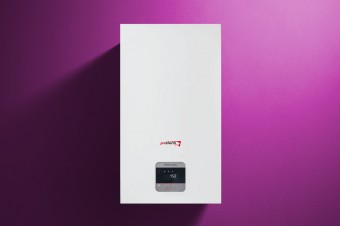